- 案例研究
Peristaltic pumps provide accurate, contained and reliable dosing for mining pilot plant
- Wardell Armstrong uses Watson-Marlow 300, 500, 600 and 700 series pumps for various applications in a pilot plant for a lead and zinc mining project in Italy
- Peristaltic pumps provide accurate, contained and reliable reagent dosing, pH control and slurry transfer between flotation stages and milling stages
- Pumps were selected for their high chemical resistance and capability of dosing very small amounts per minute
Engineering and mining consultancy company Wardell Armstrong International Ltd used a range of peristaltic pumps from Watson-Marlow Fluid Technology Solutions (WMFTS) in a pilot plant for a lead and zinc mining project.
The purpose of the testwork conducted by Wardell Armstrong was to produce bulk lead and zinc concentrates for downstream testing for Vedra Metals on their Gorno project in northern Italy. Vedra, a joint venture between Appian and Altamin, claims Gorno will be the first metal mine in Italy in 40 years and is aiming for large-scale clean zinc and lead concentrate production in 2024.
Renewable energy technologies require a wide range of minerals and metals. Zinc provides corrosion protection for the steel used in wind turbines, and also in smaller amounts in solar power plants and renewable zinc batteriesLead batteries play a vital role in wind and solar power energy generation, renewable energy storage, as well as lead-acid batteries in electric vehicles.
The demand for metals such as zinc, lead, silver, and aluminum is expected to increase rapidly over the next few decades to meet the challenge of the low-carbon transition.
Wardell Armstrong’s successful pilot plant was a significant step towards Vedra’s lead and zinc project becoming a reality and an important new source for lead and zinc.
Chemical resistance
For the bulk concentrate production runs, Wardell Armstrong used 12 Watson-Marlow 300, two 500, six 600 and three 700 series pumps for various applications. The small throughput pumps were used for reagent dosing and pH control whereas the larger throughput pumps were used for slurry transfer between flotation stages and milling stages.
Highly chemically resistant Watson-Marlow 300s were used for selective reagent dosing in all applications including flotation collectors and depressants. For this project, reagents including copper sulphate, sodium silicate, zinc sulphate, sodium hydrosulphide, methyl isobutyl carbinol, sodium isopropyl xanthate and lime (calcium oxide) were used.
Dominic Conybeare, Principal Metallurgist at Wardell Armstrong, said: “The 300s were used for dosing of collectors, depressants, frothers and also reagents for pH control.
“Dosing in very small amounts, often a couple of millilitres per minute, requires pumps that can easily and quickly be adjusted – the Watson-Marlow pumps used here do just that. Fast and easy RPM adjustments can be made to quickly adjust dosages to the required point on the circuit. Accuracy is also very important and the ability to track and record dosing is vital.
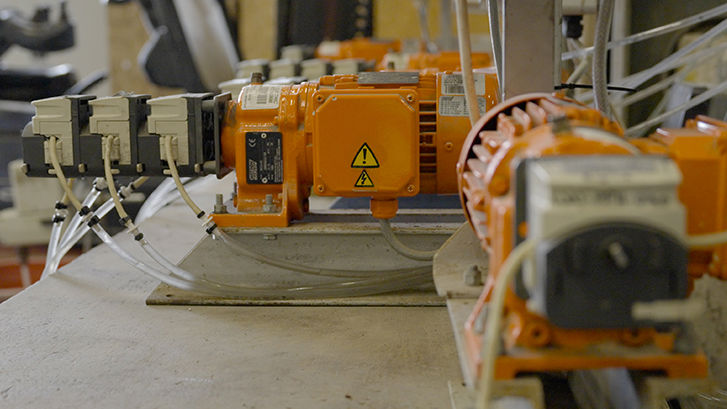
300 series flip-top pumpheads were used for reagent dosing in Wardell Armstrong’s pilot plant for a lead and zinc mining project
“We have been using Marprene® tubing from Watson-Marlow and have had no problems with corrosion with the chemicals we have been using.
“Watson-Marlow 500 pumps are used for lime dosing and provide us with consistent flowrates which is important for keeping the pH within the desired ranges for the targeted minerals.
“The three Watson-Marlow 700 pumps were used where slurry transfer rates were highest. This included to both the lead and the zinc rougher flotation banks.
“Six Watson-Marlow 600s were used as slurry pumps where mass flow was lower, but still significant. This included between rougher and cleaner flotation stages, and between cleaner stages within the same circuit. Slurry coming from the lead circuit in particular has a relatively high density, so it is important that these 600 series pumps can handle dense slurries without blocking.”
From pilot plants to reality
Pilot plants like this from Wardell Armstrong test the equipment, chemical engineering methodology, and operations on a small scale before full production.
Conybeare added: “The main benefit of pilot plant testing is to provide metallurgical proof that what has been achieved at a laboratory scale, using a sample a few kilos in mass, in terms of final concentrate grade and recovery can be successfully scaled up, using samples a few tonnes in mass, without detriment to the final outcomes.
“We are also asked for pilot plants when clients need large quantities of concentrates produced for further downstream processing, like environmental testing and thickening/dewatering testwork.”