- Case Study
- Fruit juice manufacturer SOKO changes to Bredel 25 hose pumps for reliable handling of viscous peach concentrate
- After switching to Bredel, SOKO now transfers peach concentrate quicker and more reliably compared to the previously used pump from a different pump manufacturer
- Bredel hose pumps have contributed to a more efficient production process, with reduced energy costs and better hygiene
Bredel improves efficiency, reduces costs and further enhances SOKO’s hygiene standards
Fruit juice manufacturer SOKO Gorica Ltd has increased the efficiency of its production process by replacing a pump that failed to transfer highly viscous peach concentrate with reliable Bredel hose pumps.
SOKO produces over 30 million fruit drinks a year with a process based on high-capacity automatic equipment and certified with an ISO 22000 quality management system. But due to a pump from another manufacturer being unable to handle the viscosity of the peach concentrate, SOKO had to revert to manually transferring the product, adding water and reprogramming software to adjust the recipe. This slowed down the process at SOKO’s production site in the Republic of North Macedonia as more time was spent on preparing production and the recipe.
Peach concentrate of 32 Bx (degrees Brix) and a volume of 1,14 kg/m3 (kilograms per cubic metre) was not being pumped from the aseptic drum, because the viscosity was too high for the pump size to handle.
Unhappy with the support it received from the pump manufacturer, SOKO contacted Watson-Marlow Fluid Technology Solutions (WMFTS) to discover what alternative pump solutions it could offer. WMFTS recommended a Bredel 25 peristaltic hose pump with an F-NBR food contact hose (compliant to EC1935/2004 and FDA 21CFR177.2600 and meets 3A standards) for the application of unloading fruit concentrate and puree from an aseptic drum to a production process tank. This involves a recipe of 20 kg of juice concentrate mixing with water and additives (vitamin C, sodium citrate, aroma), depending on what juice is being produced.
Alan Varelija, WMFTS sales engineer for the Balkans region, said: “I wanted to assure the customer that our solution would work, and after consultation with SOKO and our experts, we decided to send one of our demonstration pumps for a trial at SOKO. The results of the trial were exceptional, so the customer was left with no doubts about the purchase.”
Bredel enables quicker transfer times
SOKO is using the Bredel pumps for handling highly viscous peach and banana concentrates (4000-5000 cP), as well as other fruit concentrates (approximately 3000 cP). Since purchasing the Bredel pumps, SOKO’s preparation time is shorter with better hygienic conditions in a more efficient process compared to the manual preparation adopted when the previously used pump failed to transfer peach concentrate.
As the peach and other fruit concentrates are now being transferred quicker, SOKO is using less energy and so has reduced its energy costs. The Bredel 25 also does not vibrate like the previously used pump, which affected the stability of surrounding infrastructure at the production site.
Nikola Karanfilovski, Technical Manager at SOKO, said: ‘’With the previous pump we didn’t manage to pump very viscous peach concentrate from drums. This problem meant we had to prepare recipes manually, adding water and reprogramming software to adjust all ingredients.
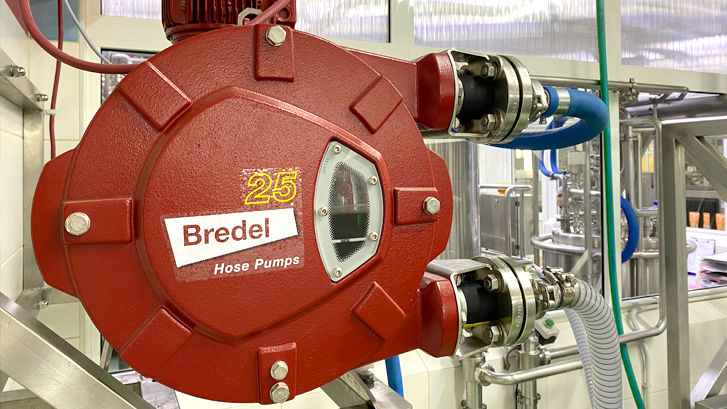
“With Bredel, pumping is smooth and we don’t have the manual time-consuming job. We can now finish recipes with simpler manipulation, with better hygienic conditions, and in a much faster time than before.”
Using direct coupled technology, Bredel combines the reliability of long-coupled pumps with the compact footprint of close-coupled pumps.
Benefits and features of Bredel 25:
- Pumps viscous and abrasive slurries and pastes, up to 80% solids in suspension
- Repeatable volumetric accuracy of +/- 1%
- Max flow: 2,740 litre/hour
- Capacity: 0.300 litre/rev
- Max discharge pressure: 16 bar
- Max fluid temperature 80C
SOKO Gorica Ltd exports 95% of its annual production to 30 different countries, including the US, Australia, New Zealand, United Arab Emirates and multiple nations in Europe.