- Case Study
Chemical metering pump
-
Qdos 30 pump proves ideal for dosing phosphorous coagulant iron III chloride
-
Maintenance time and spare parts reductions help deliver rapid ROI
-
More Qdos applications now planned at this plant and others in the company
Qdos pump replaces three diaphragm pumps at major water treatment plant
The water treatment plant at Riepe, in the East Frisia region of Lower Saxony, has replaced three diaphragm pumps with a Qdos series peristaltic pump from Watson-Marlow Fluid Technology Group (WMFTG). Dosing phosphorous coagulant iron III chloride for over a year, the Qdos 30 pump has not only cut capital equipment costs, but introduced significantly reduced maintenance and repair costs.
The Oldenburgisch-Ostfriesischer Wasserverband (OOWV) is a regional water association in the East Frisia region of Germany that not only supplies clean drinking water, but purifies the waste water from more than 500,000 people through 46 water treatment plants. "Besides household waste water, we also have a relatively large amount of waste water from industrial areas,” explains Plant Manager Klaus Janssen. “For this reason, the phosphorous levels in the inflow water are relatively high, at around 15 mg/l on average. However, our prescribed phosphorous limit at the point of entry is 2.0 mg/l, although we are in fact striving to not exceed the target limit of 0.5 mg/l.”
Diaphragm pump issues
In order to achieve this reduction, the waste water facility uses chemical coagulation, which converts the phosphate solution in the water into insoluble phosphate compounds that can then be isolated. At Riepe, one diaphragm pump supplied the coagulant from underground storage containers into the holding tank, with the actual dosing handled by two further diaphragm pumps – one in constant use and one in standby mode in the event of a failure. Indeed, failure was an increasingly common outcome as the pump diaphragms were often corroded by the chemical coagulants, making replacement necessary.
"The diaphragm pumps also produce a strongly pulsating flow which, after some time, would lead to signs of wear and tear on the fittings and valves,” says Mr Janssen. “The maintenance work started amounting to several hours per month; moreover, we had to hold a whole range of spare parts in stock, including diaphragms and valves.”
A further problem with the diaphragm pumps was suction. Air would be drawn in, which could jam the valves meaning that the diaphragm pumps were unable to prime and pump. As a result, the phosphorous limits discharged from the plant increased and, in the worst case, meant that the relevant authorities had to be notified. To avoid this, emergency operations at night or during the weekend were becoming more frequent.
The problem occurred most often whenever the stock of coagulant was replenished. Here, the chemical dosing lines had to be manually flooded with water to enable the diaphragm pumps to operate.
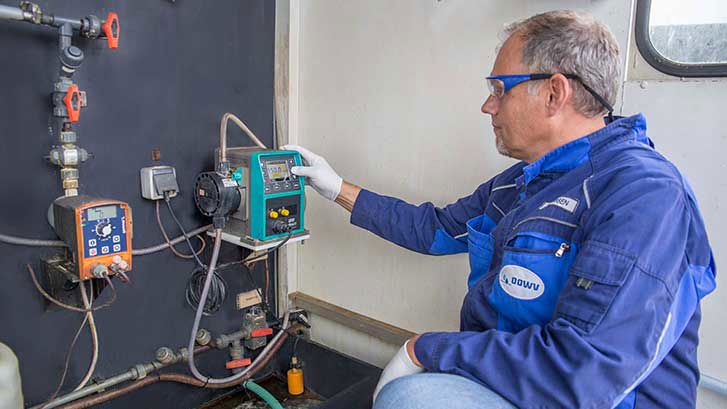
Qdos pump replaces three diaphragm pumps at major water treatment plant
High phosphate levels? No problem
The new Qdos 30 peristaltic pump at this site doses at 150ml/min, although it offers a maximum flow rate of 500ml/min – more than enough for occasions when there are high phosphate levels in the water. The single Qdos pump is able to draw the iron III chloride directly from the storage tank, which means that a holding pump, the standby pump and, the holding tank, plus associated float switches and electronics, are no longer necessary.
“While the accuracy of the diaphragm pumps declined over time as the diaphragms became corroded and worn, the Qdos pump is extremely accurate, so we’ve able to reduce the frequency of recalibration."
Complete reliability
In total, Mr Janssen estimates that the Qdos pump has led to an impressive time saving of between two and five hours per month. "By relieving us of this workload and the saving on spare parts, the investment has paid off very quickly.”