- Case Study
- ASA Spezialenzyme GmbH has selected a FP50 from Flexicon Liquid Filling for filling and stoppering vials in the microlitre range
- The compact peristaltic system enables rapid conversion between batches and is easy to scale up from small volumes at the early stage to large volumes at a late stage
- The filling and stoppering system processes up to 25 vials per minute with accuracy of ±1%
Maximum accuracy and flexibility for filling and stoppering
In its search for a for Good Manufacturing Practices (GMP)-compliant solution for filling and sealing vials in the microlitre range, ASA Spezialenzyme GmbH chose a FP50 from Flexicon Liquid Filling.
The compact peristaltic system for filling and stoppering saves space in the cleanroom and provides gentle and very precise filling of small quantities. Thanks to its versatility and the use of custom-made Flexicon single-use components, the new filling line enables rapid conversion between batches and simple adaptation to projects with larger filling quantities and vials.
ASA Spezialenzyme, based in Wolfenbüttel, Germany, specialises in the production and distribution of enzymes, microbial cultures and other innovative biotechnological products for various sectors ranging from food and beverage to paper and pulp. The company produces special enzymes, such as a newly developed adjuvant for use as an active enhancer in promising novel vaccines, including for hepatitis B and Chagas disease which are currently in the pre-clinical development phase.
A sterile process has been designed and installed in accordance with current GMP standards for the processing of the liquid-formulated adjuvants. According to GMP guidelines, high-risk operations, such as aseptic filling of sterile products, must be carried out in a class A environment. By using a Laminar Air Flow (LAF) workbench (Class A) with glove ports installed in the clean room (Class B), the risk of contamination with microorganisms, particles and pyrogens is minimized.
"After production, the liquid is first filtered in batches and transferred into a pre-sterilized bag. Then the fill/finish operation takes place, filling 500 microlitres into pre-sterilized 2R vials, before the vials are stoppered and crimped," explained Marc Schreiber, a researcher at ASA Spezialenzyme.
"Previously, we used a semi-automatic filling system for such small quantities, in which the stoppering was done manually. For this project, however, a fully automatic filling and closing process had to be installed because the vials must be stoppered as quickly as possible for regulatory reasons. In order to guarantee maximum flexibility for future projects, the new fill/finish system should not only offer a certain range of fillable volumes, but also allow for rapid conversion between batches."
The FP50 from Flexicon, part of Watson-Marlow Fluid Technology Solutions, was the perfect solution. This fully automated system processes up to 25 vials per minute. The FP50 is particularly suitable for the production of small and medium batches in pharmaceutical research and development, biopharmaceutical development laboratories and for clinical trials. All materials and surfaces comply with GMP standards for aseptic filling for simplified validation.
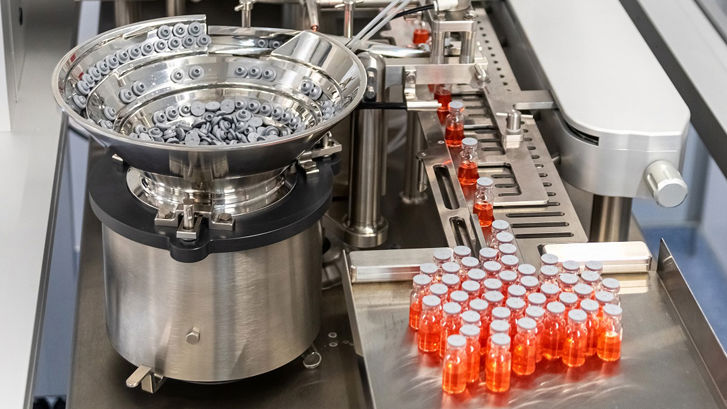
Higher accuracy without drift
The filling is carried out by a peristaltic pump with accuracy of ±1%. Stoppers can be inserted completely or partially in the case of freeze-dried products. Operation is via an easy-to-clean control panel located outside the LAF. The pump’s unique design reduces pulsation to a minimum, allowing faster dispensing rates. This system enables a scalable and transferable process for the development and production of new preparations.
A big advantage for ASA Spezialenzyme is that the compact FP50 takes up little space in the cleanroom and the feed tray can be placed straight or laterally (L-Form). When changing to larger or smaller vials and stoppers, only two format parts need to be changed.
Since the installation of the new filling line, ASA Spezialenzyme is very satisfied with the accuracy and reliability of the Flexicon FP50. The process validation went smoothly due to the extensive Installation Qualification (IQ) and Operational Qualification (OQ) documentation and ASA Spezialenzyme is also more than satisfied with the performance in operation.
"We process an average of one batch per week with 600 vials of 0.5 mL each," said Marc Schreiber.
"Our GMP samples during filling support this high accuracy from the beginning to the end of the batch, there is no drift.”
Calibration for starting a new batch is also quick and easy.
"We usually do three to five calibrations at the start of a batch or the start of the working day. By the second dose, we usually have achieved our required filling accuracy," said Marc Schreiber. "This allows us to minimize product loss during calibration."
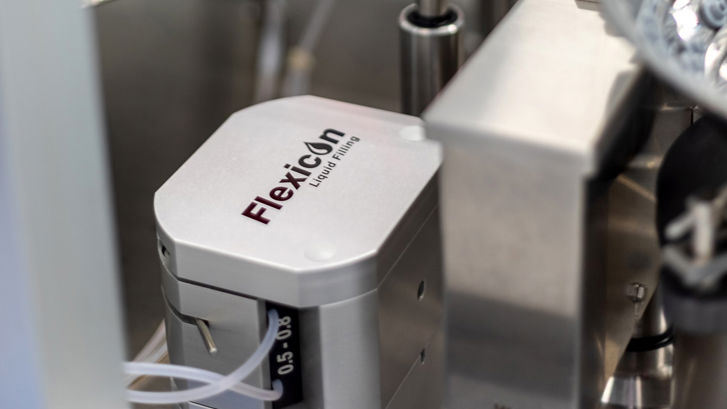
Flexibility to scale up
The company’s special enzymes are also protected due to the FP50’s simple operation and low pulsation.
Marc Schreiber said: “The gentle filling of the peristaltic system gives us security for future projects, for example when it comes to filling sensitive antibody vaccines. Just as important is the versatility of the system: very few filling systems can offer volumes as low as 0.5 mL. The FP50 with its wide filling range will also enable us to switch to larger vials at a later stage.”
This high flexibility is also made possible using Flexicon's asepticsu fluid path solution. This pre-sterilized and double-packed single-use kit includes all fluid contacting components during the filling process, such as bags, hoses and connectors, as well as the filling needle.
As both equipment and consumables come from a single source, ASA Spezialenzyme can be confident that all components are perfectly matched to each other and thanks to the versatility of the Flexicon FP50, it is future-proof.
"The single-use sets enables us to have short set-up times and thanks to the flexibility of the system, we can also easily fill larger volumes in future projects, for example the entire product, not just an auxiliary material," said Marc Schreiber.
Flexicon Liquid Filling systems for the pharmaceutical sector
Solutions for you
To learn more about our solutions for your applications please