- Case Study
Single use technology
A Cancer Research facility in Hertfordshire is among a growing contingent of clinical trial sites that have adopted fill/finish single use fluid path technology from Watson-Marlow Fluid Technology Solutions. Used in conjunction with two Flexicon FP50 automated filling and stoppering machines, fill/finish has helped the Biotherapeutics Development Unit (BDU) at South Mimms to eliminate the need for cleaning validation and simplify traceability of applied product contact components.
The BDU is a modern, MHRA licensed, fully GMP-compliant, 2000 m² facility that is engaged in the process development and production of novel Investigational Medicinal Products (IMPs) for phase I clinical trials sponsored by Cancer Research UK.
“Put simply, we’re a clinical trial supply unit within the charity, and we have our own filling lines in a sterile environment,” explains Deputy Production Manager, John Emerson. “As a result, exploiting the benefits of disposable, single use technology such as fill/finish made perfect sense.”
Lower risk
Fill/finish is a sterile, single-use fluid path perfected for aseptic filling. Used in combination with Flexicon filling machines it helps eliminate the risk of contamination in high purity filling applications. Importantly, single-use technology simplifies the validation process, making it the preferred solution over traditional hard piped systems with piston pumps that require complex cleaning validation.
“Thanks to the adoption of fill/finish we have benefited in a number of ways from its the inherent design characteristics,” confirms Mr Emerson. “As the liquid being filled is not in contact with any mechanical parts, permanent pipework or the external environment, there is no risk of cross contamination. In terms of traceability, all of the documentation is provided with the validation pack from Watson-Marlow, which makes our job much simpler. Before we had fill/finish we were either performing manual pipetting or using external resources.”
Single use technology transforms the way filling lines are used, ensuring systems are kept clean and free from contamination. In fact, sterility is guaranteed as all parts are double bagged and pre-sterilised using a validated gamma irradiation process. This eliminates the need for costly laminar air flow assembly areas, autoclaves and labour for the on-site assembly and sterilisation of filling accessories. Once the filling process is complete, users simply remove the fill/finish unit.
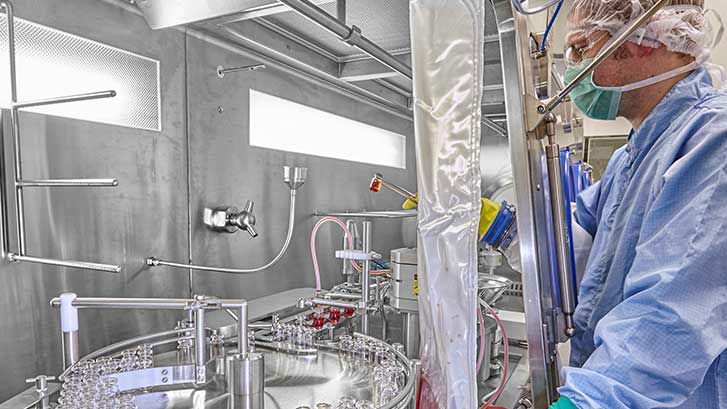
Flexicon Cancer Research
Quick and easy
“We order using a single part number, which simplifies inventory management, and the system arrives pre-configured so we are ready to go,” says Mr Emerson. “Everything is fully integrated with standard connections, so set-up time is virtually zero.”
At the heart of fill/finish is Watson-Marlow’s Accusil platinum cured silicone tubing, the only silicone tubing optimised for Flexicon fillers. Engineered specifically for post-irradiation dispensing stability and manufactured in ISO 14644-1 Class 7 cleanroom conditions under tight tolerances, Accusil is also post-cured for lowest extractables and features laser etched lot data. Importantly, the tubing helps ensure superior filling accuracy of ±0.5% is achievable on volumes higher than 1ml, thereby preventing costly overfilling.
“We fill vials between 2 and 50ml, although 5ml is probably our most common size,” says Mr Emerson. “A batch is usually 5 or 10 litres, which means filling 1000 or 2000 5ml vials. It’s important we don’t overfill.”
Solutions for you
To learn more about our solutions for your applications please