- Case Study
Reducing energy usage and greenhouse gas emissions
Executive summary
This article focuses on controlling bacterial growth in papermaking with the addition of lime which contributes to less slime formation and decreases fatty acid production.
- Peristaltic chemical metering technology can help cut gas consumption, water usage and greenhouse gas emissions
- An important aspect of pulp production is to ensure neutral pH of pulp with the addition of lime
- Only by investing in the latest technologies can the industry continue complying with strict and ever-tightening environmental regulations
Conclusions will be drawn from measurements where the correlation between drying section temperatures and lime dosing has been proved. The resulting reductions in energy consumption and emissions will lend support to the outcomes identified.
Introduction
Papermaking uses large volumes of water. 90% is used for cooling and 10% as process water. Fibre is mixed with water at the stock preparation stage of the process to create pulp. This step is followed by forming and dewatering stages, where vacuum is applied to drain the water. Any remaining water in the product is evaporated in the drying section, most often by gas-heated ovens or steam-heated drying cylinders.
The paper drying section consumes most of the energy in the manufacturing process and contributes to 68% of the total greenhouse gas emissions for the sector. However, increasing performance in the dewatering stage delivers the potential for less water to be heated and evaporated in the drying section.
To enhance dewatering processes additives are used to increase drainage of the paper fibres. The calcium carbonate content of the raw material also has a significant influence on dewatering, an area which seems underestimated by most process technologists.
The problem
The reality is that the forestry industry contributes 5% to global greenhouse gas emissions and uses 2% of the world’s energy industry-wide. As a result, pulp and paper mills face strict and tightening regulations towards environmental issues. Apart from ambitious water reuse targets emissions need to be reduced significantly, which challenges the future profitability of many paper mills.
The solution
The deployment of accurate chemical dosing technologies at paper mills can deliver a significant reduction in energy usage and greenhouse gas emissions. To evaluate this theory, a Finnish multinational and global leader in moulded fibre technology for food and drink packaging Huhtamaki
OY conducted comprehensive trials. Full-scale industrial trials took place at the company’s central research facility in the Netherlands.
The dry stock material used for these trials was a mixture of recycled paper fibres with grass added.
An important aspect of pulp production is to ensure the neutral pH of the pulp by the addition of lime. Adding lime contributes to lower bacterial growth and decreases the presence of fatty acids in the pulp. This translates into less slime in the system and reduces the odour of the end product.
More importantly, closed-loop water systems, common in paper manufacturing, struggle with a high calcium load. Water evaporates at the drying section, but the calcium remains in the system, causing scale formation.
By adding the lime at the wet end, the calcium will be enclosed in the paper floc (substrate). This will lower the calcium load as the calcium leaves the manufacturing process via the end-product. This also enhances dewatering, resulting in lower drying section temperatures and lower gas consumption.
Lime is a challenge to work with, as it tends to settle, forming lumps in suspension. Diaphragm pumps are often used to add lime. However, this can cause difficulties as ancillary foot valves tend to get blocked by lime dispersion. Even after removing the foot valve and pressure-holding valve on the discharge side, diaphragm pumps do not deliver a constant flow. As the accuracy of the quantity of lime dosed has a significant impact on the process performance and end-product quality, it is critical to select the optimal dosing pump for the task.
For the trials at Huhtamaki’s site, a Qdos 120 peristaltic chemical dosing pump from Watson-Marlow Fluid Technology Solutions was used to deliver the lime before dewatering the paper pulp.
Dewatering was far more effective, resulting in an increase of 2.5% in dry solid content
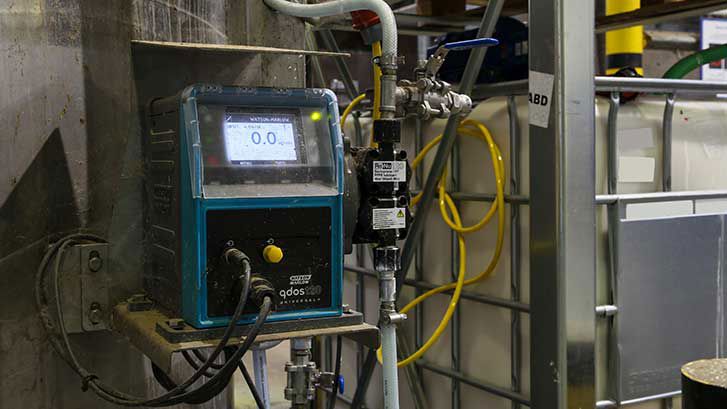
The technology
The selection of a chemical dosing pump often has a significant impact on the efficiency of a water treatment or manufacturing process. According to the specification sheets, most chemical dosing pumps deliver similar performance, although this test data is often based on ideal circumstances, which are rarely the case in practice. In truth, process conditions vary, and end-users like to install a dosing pump at the plug and play level into their process.
Qdos pumps deliver accurate flow, despite changing process conditions, and do not require additional ancillaries like inlet and pressure-holding valves. This lowers the cost of maintenance and process downtime due to clogged valves.
Huhtamaki recognised the issues with diaphragm pumps some years previously and decided to participate in the development of Qdos peristaltic metering pumps for many paper pulp duties. Since the adoption of this new technology, various process enhancements have been made, achieving increased efficiency, improved product quality, safer maintenance and significant savings on chemical usage.
Driven by Huhtamaki’s ongoing ambition to be the best-moulded fibre packaging company worldwide, it decided to establish a project to bring down its greenhouse gas emissions to a minimum, and maximise the reuse of its process water.
The project set out to optimise the calcium load in their system and impact on the company’s CO2 emissions. By dosing lime with high accuracy, Huhtamaki succeeded in achieving optimal control over the pH. The trial proved that the dewatering stage was far more effective than it had been, resulting in an increase of 2.5% dry solid content at the entrance of the drying section. Moreover, less water had to be heated up to 100C and evaporated.
There is a direct correlation between the dry solid content at the entrance to the oven and the required oven temperature. By accurately metering lime to the pulp, Huhtamaki succeeded in lowering the average oven temperature throughout the trial.
Summary
Due to the nature of the operation at Huhtamaki (24/7 for more than 350 days a year), this relatively modest decrease had a significant impact. A lowering in oven temperature of 15C correlates to a 3% reduction in gas consumption and, consequently, 3% reduction in greenhouse gas emissions. This equals a reduction of 18,000kg in carbon emissions per oven, per year, delivering a return on investment in just four weeks.
A lowering in oven temperature of 15C correlates to a 3% reduction in gas consumption and 3% reduction in greenhouse gas emissions. A return on investment was delivered in just four weeks.
Additional benefits in the addition of lime include higher machine throughput (estimated at 5%) due to lower equipment pollution levels; less product shrinkage thanks to lower oven temperature; low product odour and lower odour emissions.
Any future research or development of chemical dosing equipment should focus on ultra-low flow. The new array of nano-scale high-performance chemicals will make an entrance into the paper and pulp industry in the near future. With this in mind, high precision chemical metering will be a necessity as the industry strives for fully closed-loop water systems and zero emissions.
Solutions for you
To learn more about our solutions for your applications please