- Case Study
Piezoelectric ceramics plant installs more than 50 Bredel hose pumps
- Over 50 Bredel pumps transfer abrasive slurries that form ceramics used in capacitors
- 14 more units installed in 2019
- Benefits include zero downtime and minimal preventative maintenance
A major producer of powdered materials for piezoelectric ceramics (used in electronic components) is relying on a growing number of Bredel hose pumps from Watson-Marlow Fluid Technology Group (WMFTG). To date, the company has more than 50 Bredel pumps operating at this site, with a further 14 due for delivery before the end of 2019. The pumps are used to transfer the highly abrasive slurries that form the ceramics.
The company is among the world’s first to mass produce powdered materials for piezoelectric ceramics that do not contain environmentally hazardous lead substances. To manufacture the ceramics, BaCO3 (barium carbonate) is first dispersed into a mixture of solvent and water to prepare BaCO3 slurry. The BaCO3 slurry is then wet-milled repeatedly until the appropriate grade is formed, after which it is calcined to create high-grade powder for use in electronic capacitors.
Although this process sounds straightforward enough, the abrasive nature of the fluid presents a challenge for many conventional positive displacement pumps when it comes to feeding BaCO3 slurry to the company’s bead mill. There is high risk of metal contamination when the ceramic slurry comes into contact with the working parts of the conventional pump types, and this could not be tolerated in electronic components. Additionally, excessive abrasive wear presents ongoing cost issues in terms of pump repair, maintenance and production downtime.
With these dilemmas in mind, the plant turned to the peristaltic technology deployed in Bredel hose pumps from WMFTG. In Bredel pumps, the actual pumping principle is based on alternating compression and relaxation of the hose, drawing content in and propelling product away from the pump. As a result, the fluid being transferred is only in contact with the abrasive-resistant hose, ensuring contamination-free pumping. Moreover, as the pumps are virtually maintenance-free there are no expensive seals, valves, diaphragms or rotors to wear, leak, clog or corrode.
As a result of these clear benefits, in excess of 50 Bredel pumps are currently in use at the piezoelectric ceramics factory, ranging from 25mm to 40mm in size (inside diameter of the pump element) and running at speeds of up to 40 rpm. It is anticipated that a further 14 Bredel pumps will be delivered and installed before the end of 2019.
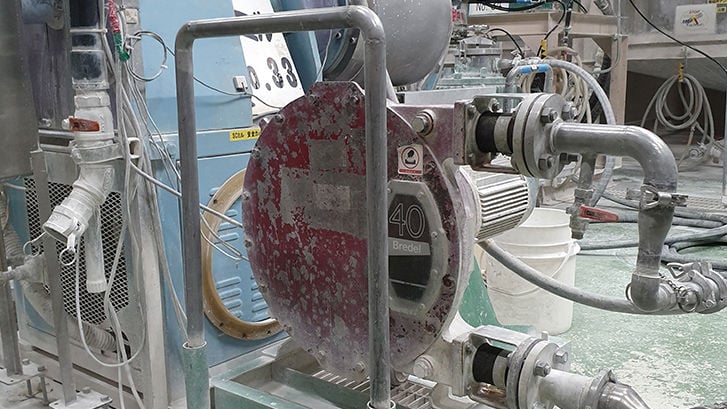
The pumps deliver the ceramic slurry to a bead mill with an integrated cooling system before it passes through a magnetic filter to remove any traces of naturally occurring iron. As the particle sizes reduce in the wet-milling process, the viscosity of the slurry changes. However, the performance of Bredel pumps is not affected by the variation in product properties.
The customer also points out that the Bredel pumps transfer the slurry gently, without air entrainment and without contamination. Importantly, there has been no downtime, while maintenance costs are minimal; the only replacement part is the hose.
At the piezoelectric ceramics plant, a long life Bredel hose element helps maximise uptime, despite the abrasive nature of the slurry, providing up to 80% more hose life. Bredel reinforced hoses are constructed from high quality compound rubbers, reinforced with individual layers of braided nylon, and finished by high-precision machining. Perfect hose compression supports long life, which in the case of the piezoelectric ceramics manufacturer, equates to around 2,000 hours (with a degree of safety factor), after which they are replaced quickly and easily as part of a preventive maintenance programme.